Why Outsource Plant Inspection Services?
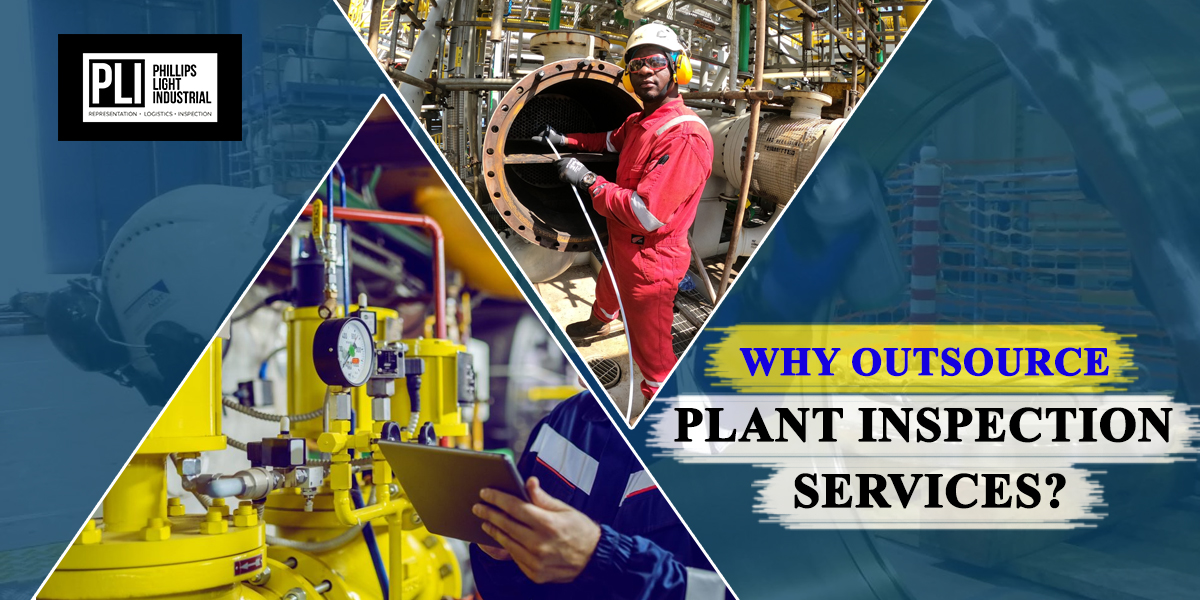
Plant inspectors ensure that all materials, equipment and processes comply with safety and quality standards. They also document all instances of non-conformance and rejected products in production reports. You can get into a plant inspection services career by taking a college course, an apprenticeship or applying directly to a company for on-the-job training. This will help you gain work experience and a good understanding of what is expected from you.
Reduced Costs
Many maintenance organizations have been outsourcing their specialized equipment repairs and routine inspections for some time now. The trend is gaining traction with smart factories that use AI to identify anomalies during in-process inspections, saving valuable time and money on unscheduled downtime.
One of the most cost-effective ways to gain valuable predictive data on plant operations is to install an asset management system that provides a central database for monitoring and analyzing plant equipment. This information can provide plant managers with insights into equipment performance, allowing them to spot problems before they damage equipment and impair safety.
Using an outsourced quality control service can be the best way to achieve this functionality. Large providers like QIMA have a global network of inspectors and a suite of technology and services that can be leveraged to deliver the most relevant solutions for a specific business. These include the ability to ramp up or down inspections as needed, the availability of the most advanced tools and technologies, and the option to deploy additional resources if a product requires extra attention.
Increased Efficiency
The increased efficiency associated with outsourcing Plant inspection services Cleveland is a tangible benefit for your business. This includes decreased worker absence, improved employee morale and an improvement in the professional perception of your company by vendors and customers.
QC providers often have global networks of inspectors with on-the-ground presence in multiple countries. This removes the need for your in-house team to travel to factory locations in other countries and mitigates the risk of managing employees in regions with safety concerns or political uncertainty. An inspection scope optimization can defer or eliminate between 30-50 percent of scheduled re-inspections, depending on the budget. In the long run, this can save your business hundreds of dollars per inspection, resulting in a positive ROI.
Increased Accuracy
Plant inspection services can be a valuable asset to a business. In addition to increased accuracy, outsourced QC providers typically have a large network of inspectors on hand. This eliminates the need for a team to travel to different locations to conduct inspections and removes any concerns about managing employees in countries that face safety issues or political uncertainty.
Inspection groups can become very effective as long as they are organized, staffed and tasked to do the best job possible at what they do. However, this isn’t always the case. Consequently, it is important to regularly assess the organization’s functions and see where improvements can be made.
Increased Flexibility
Plant inspection is an important part of a well-run manufacturing operation. Aside from the requisite inspections, it also involves monitoring the safety of workers, equipment and the environment. The latest asset integrity management tools are making it easier for plant operators to spot problems before they turn into big issues.
One of the most important reasons to outsource plant inspection services is increased flexibility. Unlike in-house quality control (QC) departments, dedicated QC firms typically have inspectors in multiple locations around the world, meaning services can be shifted in response to factory or product risk. This enables businesses to manage seasonality, ramp up or down inspections in line with sourcing trends and activate resources when needed most.
PLI Sorting also offers the highest quality inspectors and an unmatched level of customer service. They can be used to monitor sourcing, manage seasonality and minimize costs, ramp up or down inspections based on factory or product risk, and activate additional resources if a brand has a unique QC requirement.
Recommended Posts
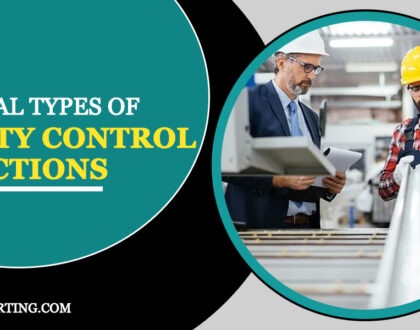
5 Critical Types of Quality Control Inspections
July 25, 2023